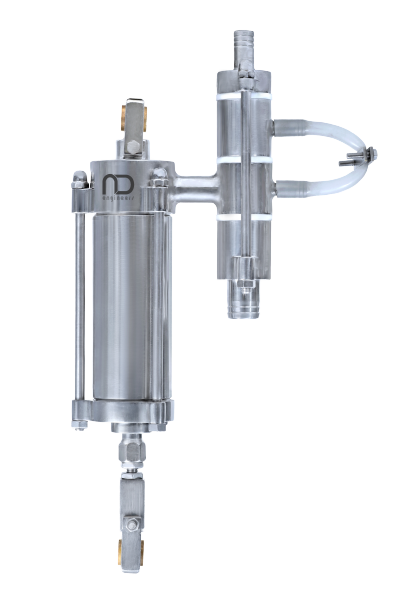
Filling needle for packaging
Title:
Enhancing Efficiency and Precision with Jacketed Filling Needles
Introduction:
In various
industries, accurate and efficient filling processes are crucial to maintain
product quality and meet production demands. One key component that plays avital role in achieving this goal is the jacketed filling needle. Designed to
ensure precise and controlled liquid filling, jacketed filling needles offer
numerous benefits in terms of product integrity, operator safety, and
operational efficiency. In this blog post, we will explore the features and
advantages of jacketed filling needles, shedding light on how they enhance the
filling process across different industries.
1.
Understanding Jacketed Filling Needles:
Jacketed
filling needles are specialized tools used for precise liquid filling in
industries such as pharmaceuticals, cosmetics, food and beverage, and more.
They are typically made of high-quality stainless steel to ensure durability
and resistance to corrosion. The unique feature of a jacketed filling needle is
the incorporation of a protective sleeve or jacket that surrounds the needle,
offering several key advantages.
2.
Temperature Control and Heat Preservation:
The jacket
surrounding the filling needle acts as a thermal barrier, enabling precise
temperature control during the filling process. This is particularly important
for heat-sensitive products that require accurate temperature maintenance to
preserve their quality and stability. The jacket helps prevent heat transfer
between the liquid and the surrounding environment, minimizing temperature
fluctuations and ensuring optimal filling conditions.
3.
Prevention of Cross-Contamination:
In
industries where stringent hygiene standards are critical, jacketed filling
needles offer an additional layer of protection against cross-contamination.
The jacket acts as a physical barrier, preventing any contact between the product
being filled and the external environment. This is especially crucial for
applications in the pharmaceutical and food industries, where maintaining
product purity and preventing contamination is of utmost importance.
4. Operator
Safety and Comfort:
Jacketed
filling needles prioritize operator safety and comfort. The external jacket
reduces the risk of accidental needlestick injuries during the filling process.
It provides a protective layer that minimizes the chances of contact between
the operator's skin and the sharp needle tip. Moreover, the jacket acts as an
insulating layer, reducing the likelihood of the needle becoming too hot to
handle, thereby ensuring a safe and comfortable working environment.
5. Improved
Filling Accuracy and Efficiency:
The precise
design of jacketed filling needles contributes to enhanced filling accuracy and
efficiency. The jacketed design allows for better control of liquid flow,
minimizing air entrapment and foaming, which can affect the accuracy of the
fill volume. By reducing wastage and optimizing the filling process, jacketed
filling needles help increase overall production efficiency and minimize
product loss.
Conclusion:
Jacketed
filling needles are indispensable tools in various industries where accurate
and efficient liquid filling is essential. Their unique features, such astemperature control, prevention of cross-contamination, operator safety, and
improved filling accuracy, make them valuable assets in maintaining product
integrity and meeting production demands. Whether it's the pharmaceutical,
cosmetic, food and beverage, or any other industry requiring precise liquid
filling, jacketed filling needles offer a reliable solution to enhance
efficiency and ensure product quality. By investing in these specialized tools,
manufacturers, suppliers, and sellers can optimize their filling processes,
leading to improved operational performance and customer satisfaction.
Filter Using Blog Tags